Why Choose a Container Dormitory in the Philippines?
A container dormitory is a modular housing solution made from shipping containers or prefabricated container units. A container dormitory in the Philippines offers a modern, scalable solution. These modular units combine affordability, durability, and rapid deployment—perfect for universities, businesses, and disaster-response teams.
Discover the advantages of choosing prefab-constructed container dormitories for your living needs in the Philippines. From time-saving construction to quick assembly, we offer custom solutions that bring efficiency, mobility, and comfort together in one space.
Fast-Track Construction
We prioritize your deadlines. Philippine container dormitories use prefabricated modules that assemble 70% faster than traditional builds. This eliminates weather delays and material shortages.
Easy Relocation
Temporary housing shouldn’t trap you in one location. These Philippine-made units ship flat-packed via standard trucks. No cranes are required. Relocate entire dorm complexes between provinces at any time.
Simplified Setup
Forget messy construction sites. The container manufacturer handles everything from permits to final inspections. You get turnkey dormitories with pre-installed wiring and plumbing.
Tailored Customization
Your needs define the design. Philippine container dormitories adapt to your space limitations and functional requirements. Choose from 50+ layout templates or request bespoke configurations. Need private bathrooms per unit? Want solar-ready roofing? Container Dormitory offers the advantage of adjusting wall placements and utility routes in 3D models.
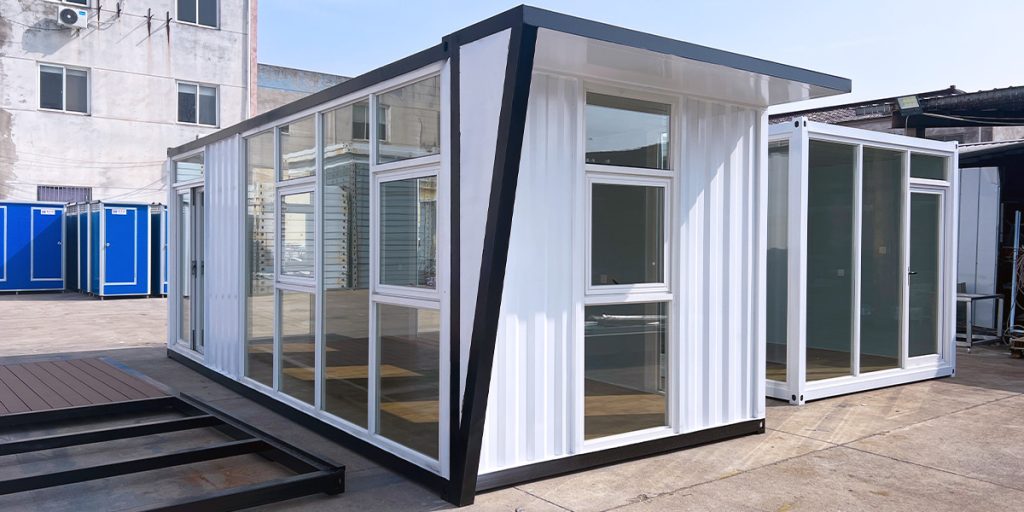
How Container Dormitories Solve Housing Challenges in the Philippines
Affordable Student Housing Solutions
Philippine universities face rising demand for student accommodations. A prefab container dormitory provides secure, tech-ready living spaces with high-speed internet and communal areas—all at half the cost of brick-and-mortar dorms.
Pro Tip: Opt for stackable designs to maximize campus space without sacrificing comfort.
Emergency Shelter for Disaster Zones
When typhoons strike, every minute counts. Container dormitories deploy within 72 hours, offering displaced families safe, hygienic shelters with solar power and rainwater harvesting systems.
Key Feature: Fire-resistant walls and earthquake-proof frames ensure safety in crisis scenarios.
Temporary Workforce Housing for Remote Sites
Need housing for oilfield workers or construction crews? Modular units with steel-framed bunk beds, shared kitchens, and air conditioning keep teams productive—even in harsh environments.
Why It Works: Units disassemble and relocate effortlessly, slashing project downtime.
What Makes Container Dormitories Durable?
Military-Grade Steel Construction | Material: Q235B stainless steel frames resist corrosion for 15+ years. |
Anti-Rust Tech: Galvanized coating + 110μ/m² paint outlasts competitors by 5x. | |
Philippine Climate Adaptations | Ventilation: Aluminum alloy windows with mosquito screens enhance airflow. |
Roof Overhangs: Optional secondary roofs combat heavy monsoon rains. |
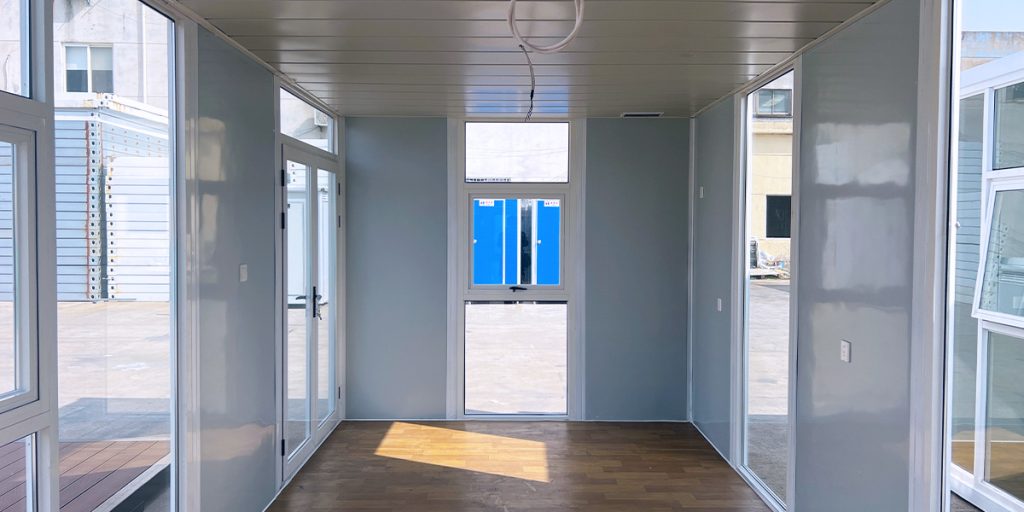
Customizing Your Container Dormitory Project
Layout Flexibility
1. Compact Units (4–6 Occupants)
Ideal for: Corporate staff housing, university faculty lodging
Standard 20ft Container (6m):
Layout:
Symmetric bunk beds (4 beds) + foldable beds (2 extra)
Central 1.2m aisle with overhead storage racks
Philippines-Specific Upgrades:
- Ventilated roof cavity + louvered side windows (heat reduction)
- Detachable mosquito nets + split-type AC (humidity control)
2. Mid-Scale Dorms (6–12 Occupants)
Ideal for: Construction camps, student housing clusters
Standard 40ft Container (12m):
Zonal Design:
Sleeping Zone: 8 bunk beds with under-bed lockers
Common Area: Foldable dining table + vertical storage cabinets
Sanitation Hub: Dual showers with typhoon-proof drainage
Monsoon Adaptations:
- 2m extended eaves (rain/UV protection)
- Corrugated steel reinforcement (120kph wind resistance)
3. Community Clusters (12+ Occupants)
Ideal for: Disaster relief hubs, island resort staff villages
Modular Configuration:
Cross-Stacked 40ft Units:
Lower Level: Communal kitchen (induction stoves) + laundry zone
Upper Level: 4-person private cabins with balcony access
Philippines-Centric Features:
- Central courtyard (natural ventilation)
Emergency Mode:
Rapid conversion to isolation units (airtight partitions + negative pressure systems)
Plug-and-Play Features
1. Base Configuration
Every Container Dormitory Philippines unit ships pre-installed with:
Lighting: LED strips + motion-sensor exterior lights
Power: 8x grounded sockets (220V, typhoon-proof wiring conduits)
Security: Heavy-duty steel doors + deadbolt locks
Ventilation: Pre-drilled wall vents
Philippines-Specific Defaults:
- Corrosion-resistant electrical panels (humidity protection)
- GFCI outlets near bathrooms (flood-risk zones)
2. Add-On Modules
Custom Container Dormitory Philippines units for local needs:
(1)Energy Independence
Solar Kits: 1.5kW roof-mounted panels + lithium batteries
Wind Resistance: Hurricane-rated mounting brackets
(2)Sanitation Upgrades
Septic Tanks: Fiberglass 500L tanks with anaerobic digesters (ideal for off-grid islands)
ADA Ramps: Foldable aluminum ramps (1:12 slope, dockside, or mountain terrain)
(3)Disaster Resilience
Storm Mode: Bolt-on typhoon shutters
Flood Adaptation: 40cm elevated steel stilts (coastal/Delta regions)
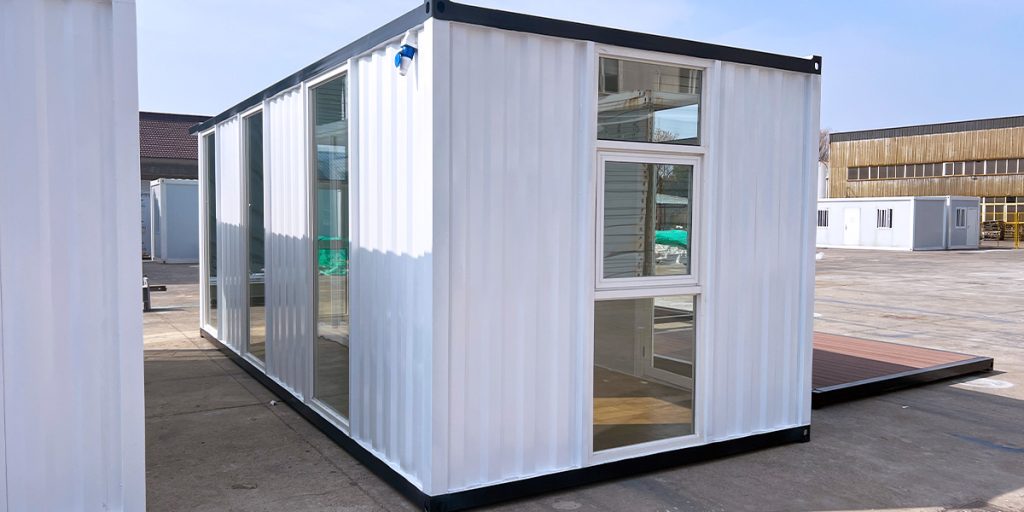
Project Construction Process
1. Precision Engineering
Every Container Dormitory Philippines unit starts with 3D modeling:
Typhoon Resistance: Simulates wind loads
Structural Integrity: Reinforced corner castings + diagonal cross-bracing for seismic Zone 4 (Philippine fault lines)
Local Adaptation: Design tweaks for coastal salt spray corrosion and monsoon rain angles
2. Factory Assembly
Container Dormitory Philippines units are crafted with aerospace-grade manufacturing:
Automated production lines: flexible production, Industry 4.0 integration
Laser Cutting: Millimeter-scale precision for door/window cutouts
Material Prep: Sandblasted steel coated with 3-layer epoxy-zinc (15 years of rust prevention)
3. Quality Testing
Units undergo water pressure tests and seismic simulations. At the same time, third-party inspection reports can be provided upon customer request.
FAQs
1. What materials ensure durability in Philippine climates?
Container Dormitory Philippines units use triple-layer engineered materials:
Walls/Roof: color-coated steel sandwich panels (0.018 W/m·K thermal conductivity)
Flooring: Marine-grade plywood + anti-slip galvanized steel
Structural Frame: high-strength steel with hot-dip galvanization
2. Can these units survive extreme heat?
Yes! The insulation layer and air conditioning system can keep the indoor temperature comfortable.
3. How long does installation take?
Three workers assemble 50 sqm/day—no heavy machinery needed.
4. Are permits required?
Most provinces classify container dormitories as temporary structures, simplifying approvals.
5. Can we customize for tropical aesthetics?
Yes! Container Dormitory Philippines offers climate-smart customization。
6. Can we expand units post-deployment?
Container Dormitory Philippines offers plug-in scalability, all components maintain structural integrity through 10+ reconfigurations.
7. How are units transported to remote islands?
Container Dormitory Philippines logistics include:
Packaging: Flat-packed components
Shipping: Vessel compatibility
Last-Mile Handling: Helicopter sling capacity for mountain sites, Barge-mounted cranes for coastal deployments
It is recommended to contact a local logistics company to negotiate a better price.
ZN House has completed thousands of modular housing projects, earning a strong reputation in over 50 countries. Our expertise in prefab housing, combined with customizable design options, allows us to provide container dormitories that meet the unique needs of clients in the Philippines and beyond. Whether for temporary workforce housing or permanent structures, ZN House guarantees high-quality, safe, and sustainable solutions backed by extensive industry experience.